During a manufacturing process, a hydraulic press brake plays an important role. It’s used to push a fixed disk that rotates. It is controlled by a set of valves. The valves are used for rotating the shaft and for pushing the fixed disk. There are also automatic tool changing systems in this type of device.
Basic working principle
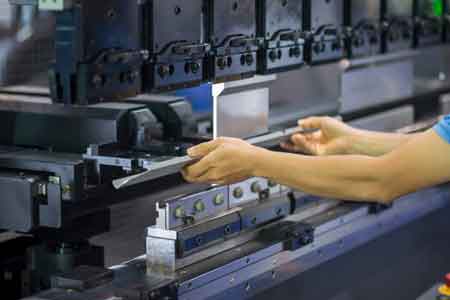
Basically, a press brake is a machine that can bend metals into different shapes. This type of machine can be used in sheet metal manufacturing industries. There are two main types of press brakes, mechanical press brake and CNC hydraulic press brake.
Mechanical press brakes are comparatively simple and easy to operate. They can handle tonnages up to two to three times more than their rated value. However, they are less accurate than hydraulic press brakes. The press brake is a must-have machine for sheet metal industry.
The hydraulic press brake is a cost-effective, versatile machine. It is used in a variety of industries, including aerospace, automotive, and industrial manufacturing. It is also a safer alternative to flywheel-driven presses.
Hydraulic press brakes use a ram to push and pull sheet metal. The ram descends and rises to press the sheet metal against the lower die. The ram is powered by a pump and valve that measure pressure and determine the amount of movement.
Control valves
Typical hydraulic press brakes have control valves to regulate the upper and lower cavities of the ram. These valves control the speed and direction of the ram, and can also act as a means of accelerating the ram.
Control valves of the present invention are especially adapted to a press brake having two hydraulic cylinders actuating the ram. However, the system can be applied to any hydraulically actuated machine.
The system includes a pressure transducer to measure the pressure in hydraulic lines serving the ram. Input signals from the transducer are used in conjunction with the processor’s internal processing to provide constant ram level control. The processor may also provide other user controlled inputs to provide desired features.
The processor also controls all solenoid actuated valves of the hydraulic circuit. In order to provide the best possible safety, the control system interlocks the hydraulic and electrical circuits. This prevents the simplification of the hydraulic and electric circuits.
Rotating a shaft while pushing a fixed disk
Using the hydraulic press to push a fixed disk has some obvious advantages. One of them is the ability to apply a constant force over a long period of time. This can be useful for heavy-duty applications where thermal damage to brake components is a risk.
The first cylinder in a hydraulic press is responsible for generating the shaft’s rotational force, and the second cylinder is responsible for pushing the fixed disk. The cylinders are matched to the fixed disk in such a way that the resulting friction forces are balanced. The resulting braking power is not as much as you would expect, but the torque generated is more than enough to keep the wheels from turning.
There are several ways to measure the temperature of a brake rotor. This is a tricky matter, and manufacturers of friction materials may prefer to perform their own temperature testing. In the case of a hydraulic press, the operating temperature is easily defined as the rotor’s temperature at the time of braking.
Automatic tool changing
Using an automatic tool changing system on your hydraulic press brake can save time and improve productivity. With a tooling changeout, you can save up to 80 percent of setup time. This doesn’t have to impact the number of part configurations you can achieve.
The press brake industry is a competitive one, and manufacturers are constantly looking for ways to improve production speed. In some cases, press brake downtime can be very significant. These issues have led to manufacturers offering solutions to help reduce tool changing time.
The tool changing process can also be a safety issue for operators. They may be at risk of breaking tools. This can be especially true if they are working with heavy tools.
Summary:
One solution is the Xpert Tool Changer system. This system integrates new tools into the magazine. It also prevents the insertion of tools that are not suitable for the press brake. This helps the operator to avoid mistakes. It also includes a cleaning nozzle that cleans the whole length of the bending table.